
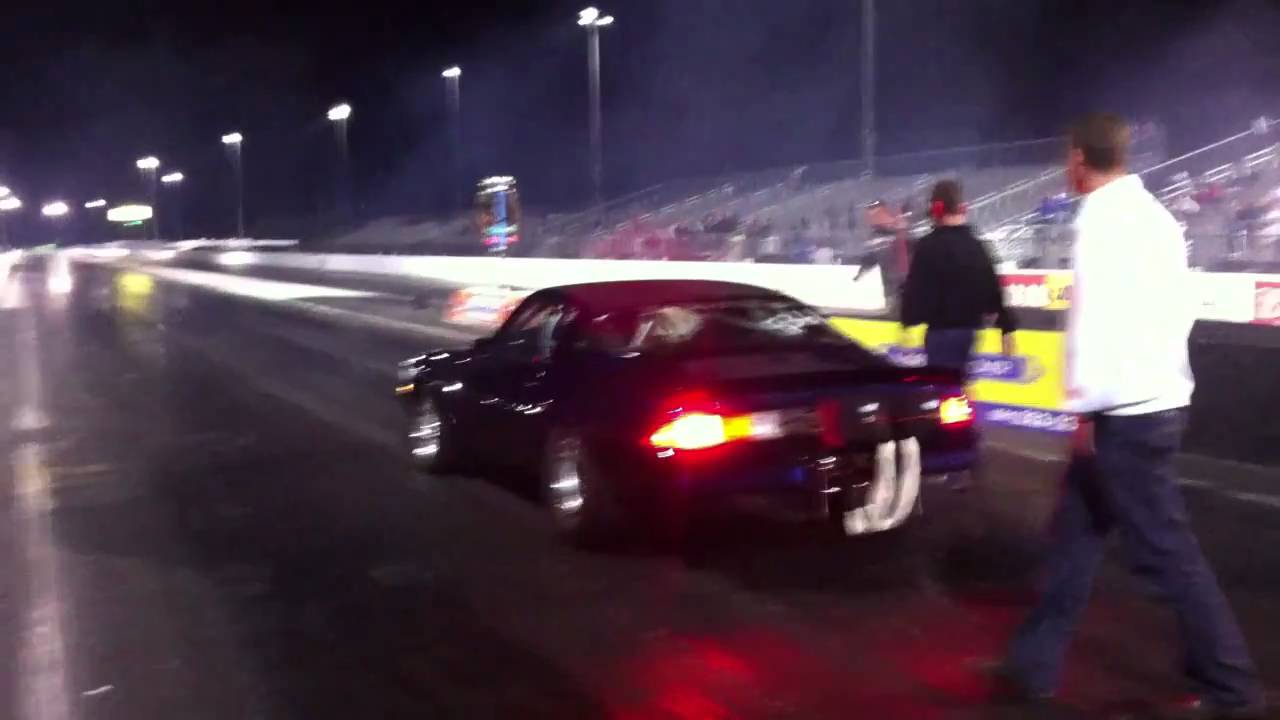
Sal, the biggest restrictions for the stock motor are the intake and exhaust. I only surf by using that, but if I do happen to look into the individual areas, theres a TON of stuff I miss!!!! The ECM then uses this information to determine the proper ignition timing per cylinder on an individual basis.I swear I miss out on a ton of posts because of that damn "view new posts" button. A processor called the EBT reads both signals and determines the exact position of the crankshaft, accurate to 1 degree.
#Stock pro charged lt1 windows
At the same time, the inner phototransistor is generating a signal for the eight windows that correspond to the top dead center of each piston. The disc is driven by the cam, so as it turns with the engine, the phototransistor reads the "on and off" of each window as it breaks the beam of light and generates a voltage for each event-a total of 720 pulses per camshaft revolution, which corresponds to one revolution of the crankshaft. The outer track has 360 windows the inner has only eight windows, but these eight windows are all of differing widths. The disc has two tracks of slots or windows cut into its perimeter. The light is broken up by a disc sandwiched between the two. Light from the LEDs excites the transistors, causing them to generate a voltage. An optical sensor made of matched pairs of LEDs and phototransistors resides in the distributor housing. Opti-SparkAnother big change from the traditional small-block design was the Opti-Spark ignition system, which incorporates two functions in one unit: It's a crank-angle sensor as well as a distributor. He says that reverse flow may not contribute that much to the engine's performance it doesn't hurt it, either, but it really limits the amount of aftermarket parts available for this engine. Karl Ellwein of Ellwein Engines-a builder who deals solely with LT1s-is a little less enthusiastic. "It just makes sense to cool the hottest part of the engine first," McKeown tells us. McKeown actually modified one of the Ford Clevor engines he built for a recent Jegs Engine Masters Competition to run a reverse-flow system. For a performance application, though, Chad Golen of Golen Engine Service and Mark McKeown of McKeown Motorsports Engineering are firm believers in reverse flow and say that the LT1 wouldn't be able to generate the power levels it's capable of without the reverse-flow design. For the type of driving the average person does, a standard-flow system does the job adequately, and without the added parts needed to make a reverse-flow system work. Their reactions were mixed but affirmed what we suspected: Reverse-flow cooling works well-better, probably, than a standard-flow system. We talked to several engine builders to get their take on reverse-flow cooling. This is because vaporized coolant can't transfer heat as efficiently as liquid coolant it essentially acts as an insulator, allowing the temperature in the area to spike. But if a steam pocket does form, the vaporized coolant can impede the flow of the liquid to that particular area of the water jacket and a hot spot will develop on the inside of the chamber-setting up a situation that can cause detonation at best, and engine failure at worst. Usually the coolant flow rate is strong enough to sweep the vapor away, constantly dousing the area with a steady stream of liquid coolant, and any vapor bubbles that did form usually condense back into the coolant stream. This is called nucleate boiling it is normal and does not pose a problem to the operation of the cooling system as long as the vapor is not allowed to accumulate. The layer of coolant directly in contact with the combustion chambers, particularly near the spark plugs and exhaust valve seats, is being vaporized. This is because the walls of the combustion chamber are much hotter than the boiling point of coolant. In any given engine, under most operating conditions, the coolant is boiling somewhere in the engine-usually in the coolant passages in the cylinder head. Reverse-flow cooling, while inherently better than standard-flow systems, requires some additional engineering for it to work properly.

So if reverse flow is so awesome, why don't all the manufacturers use it? The answer, of course, is cost.
